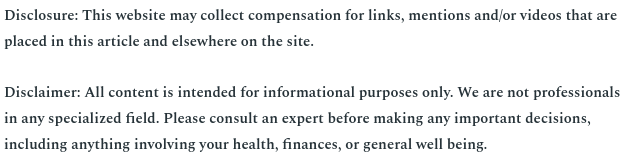
- Strategic inventory management in furniture retail is crucial for aligning stock levels with customer demand and avoiding overstock and shortages.
- Building strong relationships with suppliers enables flexible inventory adjustments, ensuring readiness for unexpected surges and standard demand fluctuations.
- Implementing RFID tagging and IoT devices enhances the accuracy of tracking goods, providing real-time insights into inventory status and location.
- Leveraging modern technology reduces inventory inaccuracies, improves operational efficiency, and elevates customer satisfaction by enabling informed decision-making.
- Continuous improvement and adoption of outlined strategies are essential for furniture retailers to thrive in the competitive market.
In furniture retail, managing inventory effectively is both an art and a science. A well-organized inventory system can be the linchpin of a successful business, directly impacting everything from customer satisfaction to profitability. This blog post will explore the common challenges faced by furniture businesses and provide strategic advice on handling these issues effectively.
Identifying Common Inventory Challenges
Overstocking and Understocking
Balancing demand and supply is crucial in the furniture industry. Overstocking leads to increased holding costs and the potential for outdated stock, while understocking can result in lost sales and dissatisfied customers. Accurate forecasting necessitates a deep understanding of market trends and customer preferences.
Inefficient Inventory Tracking
In the dynamic environment of furniture sales, maintaining an accurate track of inventory levels is imperative. Inefficient tracking systems can create discrepancies between stock levels and recorded data, leading to overstocking or understocking scenarios. Implementing advanced inventory management software that integrates real-time tracking can drastically reduce these discrepancies.
Such systems offer the dual benefits of providing up-to-date inventory data and facilitating better decision-making regarding purchase orders and stock adjustments. Adopting technology solutions for inventory management streamlines operations and enhances customer satisfaction by ensuring that popular items are always in stock.
Damage and Loss
Given the size and fragility of many furniture items, damage and loss can significantly impact your bottom line. Minimizing these risks requires stringent quality control measures, robust packaging standards, and secure storage facilities.
Seasonal Demand Fluctuations
Like many retail sectors, furniture sales can be highly seasonal. Effective management involves planning for these fluctuations and using historical sales data to adjust inventory levels appropriately.
Storage Constraints and Solutions
Furniture items are bulky and may require climate-controlled conditions to prevent damage. Leveraging a well-organized and appropriately conditioned area can mitigate some of these challenges, ensuring products remain pristine until sold.
Large storage units, while representing an investment, offer significant value through space maximization and efficiency, making them a smart choice for businesses ready to scale. Furniture companies, for instance, benefit from these units by either utilizing third-party facilities or investing in technology like automated vertical carousels or storage racks to optimize their storage capabilities. This strategic approach enhances operational efficiency and supports growth and expansion.
Technological Tools for Inventory Management
Investing in the right technology can revolutionize inventory management. Modern software solutions offer real-time tracking, predictive analytics for forecasting, and tools for optimizing warehouse layout. Such systems streamline operations and significantly reduce the risk of human error.
The Role of E-Commerce in Inventory Management
The rise of e-commerce has transformed inventory management in the furniture industry. With more consumers shopping online, having an accurate, real-time inventory system is crucial. This digital shift requires businesses to synchronize their online and physical inventory levels to prevent over-selling and understocking scenarios.
Advanced e-commerce platforms integrated with inventory management software can automatically update stock levels, send restock notifications, and predict future inventory needs based on shopping trends. This integration ensures that customers have a seamless shopping experience, increasing satisfaction and loyalty, which are vital in the competitive online marketplace.
Sustainability in Inventory Management
Sustainability has become a critical aspect of inventory management in the furniture industry. Companies are increasingly adopting eco-friendly practices, from sourcing sustainable materials to reducing waste in their supply chains. Implementing green initiatives supports environmental conservation and appeals to the growing segment of consumers prioritizing sustainability.
Furniture businesses can significantly lower their carbon footprint by recycling materials and optimizing inventory levels to minimize excess. Furthermore, sustainable practices often lead to cost savings, as they can streamline operations and reduce the need for excess storage space. As consumer awareness and regulatory pressure increase, integrating sustainability into inventory management will become not merely an option but a necessity for staying competitive in the market.
Implementing Effective Inventory Management Strategies
Regular Audits and Reporting
Regular audits are essential to ensure your inventory records match your physical stock. These should be scheduled at intervals that make sense for your business dynamics and involve spot-checking and comprehensive reviews.
Lean Inventory Techniques
Applying lean principles to inventory management can help minimize waste, reduce costs, and ensure a smoother supply chain. This might involve strategies like just-in-time (JIT) ordering, which reduces the need to hold large quantities of stock.
Supplier Relations and Inventory Flexibility
Cultivating strong relationships with your suppliers can lead to more flexible inventory management. Negotiating favorable terms that allow for adjustments based on actual demand ensures that you’re not left holding excess stock or scrambling to meet an unexpected surge in demand.
Utilizing Technology for Enhanced Accuracy
Advancements in technology play a pivotal role in refining inventory management processes. For instance, implementing RFID (Radio Frequency Identification) tagging offers unparalleled accuracy in tracking goods through the supply chain. These tags, combined with IoT (Internet of Things) devices, provide detailed insights into the status and location of inventory, enabling businesses to make informed decisions swiftly.
By leveraging such technologies, companies can significantly diminish discrepancies between recorded and actual stock levels, enhancing operational efficiency and customer satisfaction. This digital transformation in inventory management elevates accuracy and facilitates real-time decision-making and forecasting.
Conclusion
Effective inventory management in furniture requires a multifaceted approach, combining good practices with modern technology. Furniture retailers, small business owners, and inventory managers can significantly improve their operations by recognizing the common challenges and implementing the strategies outlined in this post. Continuous improvement in these practices is vital for survival and thriving in the competitive furniture retail industry.