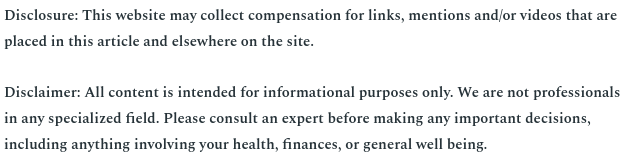
The modern American manufacturing economy is a truly vast one, and it employs many millions of people while adding a lot of value to the American economy as a whole. About $2.17 trillion, in fact, and this figure might grow in the coming years, too. How is this done? All sorts of machines and tools are used to produce different goods, from drills to welding torches to screws and laser cutter heads. But it may be noted that just building an item does not finish the work. Many goods with metal surfaces will need some touching up, and that includes roller burnishing, surface finish reamers, diamond burnishing gear, lathe tables, and the like. What is a burnishing tool used for, such as diamond burnishing equipment? Don’t forget lathes, either, which have their own important role to play.
Using Diamond Burnishing Tools
Burnishing equipment, such as diamond burnishing tools, are used to make a product’s metal surfaces complete, and this can even be done on jewelry. In general, the idea is to apply a round surface or item onto a piece of metal, and apply a great deal of pressure while rolling it around smoothly. Often, this work is automated, and to great effect. As a burnishing tool is used on metal, the smooth but intense pressure will compress the metal somewhat, and result in a surface that is hard and tough. This can greatly increase the metal’s tolerance for weight bearing or stress during its intended work. In short, burnishing can “toughen up” some metal and get it ready for a heavy work load later on.
Burnishing has a role to play with aesthetics, too. A piece of burnished metal is not just tough, but it will be smooth and may have a burnished sheen to it that’s attractive to the eye. A piece of wholesale equipment may attract buyers not only from its performance, but how it looks the part, too. An non-burnished piece of gear may not look like much. In fact, it is not uncommon for an item such as a piece of jewelry or others to be burnished again, after some years of use. Jewelry in particular can be put into rolling cylinders filled with water and metal bits, which grind away imperfections and leave smooth, polished gold and silver surfaces behind. This is the power of burnishing.
Lathes and Metal Burrs
Meanwhile, a lathe table has its own job at a manufacturing site, whether a modest workshop or a huge factory. Lathes are any device that can scrape and grind off rough, upraised imperfections on another piece of material, and the idea dates back to ancient Egypt. Hand-operated lathes have been found in archaeological sites. But today’s lathes are mechanized tables with many parts, including computers that help the lathe perform an accurate and precise job. So, a piece of wood or metal can be placed on an assembly on the lathe, and it will be slowly and smoothly “fed” to a rotating grinder surface. The RPMs of that grinder may vary, but the idea is the same: grind off upraised imperfections on the surface, and leave behind a smooth surface instead.
Why do this at all? Machining pieces of wood and especially metal can create burrs where cutting, drilling, or welding has taken place, and that’s not be desired. These upraised burrs are at best unsightly and may make a bad impression on anyone who purchases these goods. It simply looks like sloppy work. What is more, those burrs may scratch and scrape against other surfaces and items during the device’s operation, which can cause all kinds of trouble. Not to mention how burrs might snag on objects or even attract static electricity. So, lathes will grind them right off.
Any factory owner should have a working relationship with local suppliers for factory parts, and this includes diamond burnishing tools, lathe replacement parts, and even machine lube to keep everything running. This can make all the difference during manufacturing, and it may be noted that many factory owners admit to not using enough machine lube. Without it, machines may overheat or damage themselves due to friction and s scraping, which can lead to expensive shutdowns in the factory.