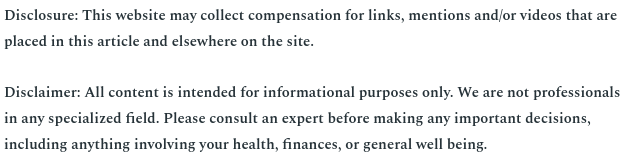
Keeping industrial equipment in good working conditions is one of the fundamental qualities of proper management. Part of this entails maintenance, repairs, and cleaning. Water blasting, steam cleaning and sandblasting are all exceptional methods of cleaning, but dry ice cleaning systems have a certain edge over the rest.
Dry ice cleaning systems build upon a cleaning technique known as dry ice blasting which was first patented in 1955. The process is fast since dry ice does not go through a liquid phase.
How Dry Ice Cleaning Systems Work?
This system operates on the same principle as a sandblaster. The only difference is instead of shooting sand from its nozzle; it sprays pressurized dry ice. The dry ice contains tiny ice particles that are shot out at high pressure. This clears out all foreign material on a surface.
When these particles of dry ice hit the surface they are cleaning, they cause the top layer of coating to shrink, which creates cracks in the surface layer. The pellets then come in contact with the warmer surface below and absorb the heat. This heat absorption causes the pellets of dry ice to turn back into carbon dioxide gas, which expands, causing the outer coating to loosen and break free.
The types of dirt removed completely by dry ice machine systems include grease, oil, adhesives, asphalt, decals, paint, tar, ink, soot, and resins.
There are other advantages of using dry ice cleaning systems which include
They Are a High-Performance Sand Blaster Alternative
Ice blasting is a great sandblaster alternative because of its non-abrasive media. This is because the dry ice particles turn back into a gas instantaneously upon impact. Therefore, as a cleaning method, it does not cause damage to the machine’s surface being blasted. This fact makes dry ice cleaning systems a better alternative compared to conventional cleaning methods.
Are a Good Alternative to Water and Steam Blasting
In addition to being an alternative to sandblasting, an ice blast machine can also replace water and steam blasting in many applications. Ice blasting is better than the alternatives because:
- You don’t have to wait for electrical parts and generators to dry out before using them.
- One does not require huge containers to hold and remove the contaminated water during or after the cleaning process.
- No moisture residue is left behind once all the foreign material has been removed. This prevents instances of rust and corrosion after cleaning.
- Cleaning boat hulls is quicker and more detailed because ice blasting discourages algae, sea slime, and mussels from reattaching. This enhances the longevity of your vessels
Environmentally Sustainable Cleaning
An ice machine is a very eco-friendly blaster that does not need environmental degrading chemicals to get the job done. The system has no secondary waste. It is thus safer for the environment, the equipment being cleaned, and the user. Ice blasting also has a positive impact on your balance sheet since it is cheaper than the alternatives.
Dry Ice Blast Cleaning Machine Safety
There are some risks that come with handling this equipment. To mitigate against them, the operator must adhere to the established protection measures and continuously review any updates made on the protective manuals.
Apart from wearing eye protection, gloves and ear protection here are some other basic safety measures
- Before blasting, make sure you inspect the blast unit, its hose, guns, and nozzles for any ruptures or damage. This prevents leaking dry ice from coming into contact with your skin.
- Never exceed the recommended blast pressure levels.
- Gases leave the gun nozzle at high speeds. Never aim the nozzle at people or where people are seated. Also, beware of particles that can be deflected from the surfaces being sprayed.
- Ensure your hoses are tightened before blasting to avoid any dry ice leaking around you. Inhaling dry ice can cause health complications to the users.
In Conclusion
These machines have outdone the pacesetters, i.e., sandblasters and steam cleaners. Dry ice cleaning has shown that you can save up to 70% compared to conventional methods without caustic agents that destroy the environment.