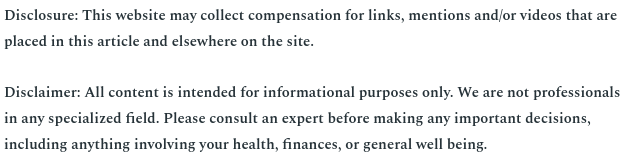
In today’s fast-paced business environment, process streamlining is essential for improving efficiency, reducing costs, and enhancing productivity. Streamlining involves analyzing and refining workflows to eliminate redundancies, reduce waste, and ensure that every step adds value. Here’s how organizations can effectively streamline their processes.
1. Identify and Map Out Processes
The first step in process streamlining is to identify all the key processes within your organization. Create a detailed map of each process, documenting every step from start to finish.
This helps in visualizing the entire workflow and identifying areas where inefficiencies and bottlenecks occur.
2. Analyze for Inefficiencies
Once the processes are mapped out, analyze them to spot inefficiencies. Look for repetitive tasks, unnecessary steps, and delays. Engage employees who are involved in these processes as they can provide valuable insights into what works and what doesn’t.
3. Simplify and Standardize
Eliminate unnecessary steps and simplify complex tasks to create a more streamlined workflow. Standardizing processes can also reduce variability and errors, making it easier for employees to follow procedures consistently. Implementing standard operating procedures (SOPs) can be beneficial in achieving this.
4. Automate Where Possible
Automation is a powerful tool for streamlining processes. Identify tasks that can be automated, such as data entry, reporting, and communication. Leveraging technology not only speeds up processes but also reduces the likelihood of human error.
5. Monitor and Optimize Continuously
Process streamlining is not a one-time effort. Continuously monitor the performance of your processes and make adjustments as needed. Use key performance indicators (KPIs) to measure efficiency and identify areas for further improvement. Regularly reviewing processes ensures they remain efficient and effective.
6. Train and Engage Employees
Ensuring that employees are well-trained and engaged is crucial for successful process streamlining. Provide training on new processes and tools, and encourage feedback. Engaged employees are more likely to embrace changes and contribute to continuous improvement efforts.
7. Leverage Lean and Six Sigma Methodologies
Adopting methodologies such as Lean and Six Sigma can provide structured approaches to process improvement. Lean focuses on eliminating waste, while Six Sigma aims to reduce variability and defects. Combining these methodologies can lead to significant enhancements in process efficiency and quality.
By implementing these strategies, organizations can streamline their processes, leading to improved efficiency, reduced costs, and enhanced overall productivity. Continuous monitoring and optimization ensure that processes remain efficient and adapt to changing business needs.
.