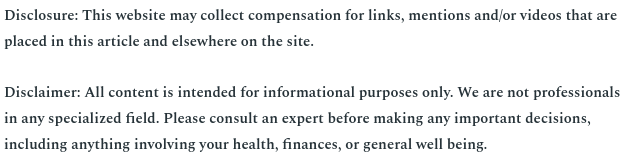
The plastics industry is very important to the American and global economy. It is the third largest industry in manufacturing in the United States. It has been estimated that every hour, about 2.5 million plastic bottles are used around the country. The good news about all of this plastic usage is that you can get more bang for your buck. Two pounds of plastic can be made to transport about 1,300 ounces of liquid. To do the same thing, you would have to use 40 pounds of glass or three of aluminum. Whether you are working with plastic cylinder tubes or are one of the plastic bottle manufacturing companies around the nation, you have two main options to get the results you want.
The two main ways to manufacture plastic cylinder tubes or plastic containers. They are injection molding and blow molding. These are very common ways to make products from plastic. Containers and other products that have been made via the injection molding method are heavier than those made with the blow molding technique. Both can manufacture products quickly and efficiently.
Typically, injection modeling is used for more solid parts and products. You can make plastic bottles and plastic cylinder tubes with this method but the walls will be thicker. Most plastic bottles and plastic cylinder tubes are made via the blow molding technique.
Another big difference is the flexibility of the product. When you use the injection molding process, the result is plastic parts or components that are more thick and rigid. If you need more flexible plastic products, blow molding may be the best option for your products. The reason for this involves both the processes involved and the starting materials each requires.
A Look at Each Process:
Here are the steps for the injection molding process:
- Create the mold. This is the most time-consuming part of the process, about 90% of the work is done at this stage.
- Melt the plastic material. The first step in the actual production is the melting of the material.
- Inject the melted plastic into your mold.
- Remove from the mold. After it has been given the chance to cool, you remove the plastic from the mold.
- Repeat.
Here are the steps for the blow molding process.
- Make the mold. While it takes less time to build the mold with this method, at least half the time will be spent here.
- Melt the plastic. Again the plastic needs to be melted. After being pressurized, it is added to the mold. It then moves through the mold and is cut off at appropriate points.
- This is a continuous process do you do not remove all of the plastic product and then start again.
- Add air to the mold as needed. This is used to force the material to expand as needed.
For both injection molding and blow molding, the costs associated with the set-up and parts to make plastic jars or plastic cylinder tubes is roughly the same. The time it takes to go from raw materials to finished product is also very similar. The difference rears its head when it comes to creating the molds. This is much more costly when you are dealing with injection molding than with blow molding.
The reason for that is that engineers need to design molding for each separate part. Every part needs to have a corresponding mold that was designed for it specifically. When companies go with the injection molding method, they often have to make large quantities of each part or product to make the process cost-effective.
The blow molding process may seem to be easier and more cost-effective but there are downsides to this process as well. If you have a need for thicker plastic cylinder tubes or jars, you may find that this method cannot create the thickness you need. The bottom line is that if you need thicker plastic parts or products and need to make a lot of them all at once, you may be better off with the injection molding process.
At the end of the day, when it comes to manufacturing plastic cylinder tube, plastic bottles, or other plastic products, there is no “one size fits all” option. You need to consider your needs when deciding which molding process will work best.