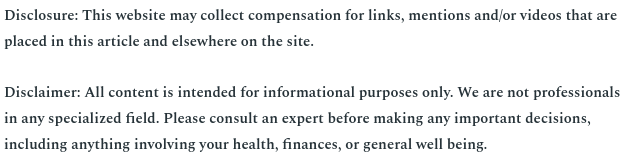
With manufacturers contributing $2.17 trillion annually to the U.S. economy, manufacturing remains one of the largest and most important industries in the country. And because of its importance, there are continuous changes and improvements in manufacturing methods. One of the most essential processes in manufacturing is material joining. So let’s explore the pros and cons of two common material joining processes: welding and mechanical joining.
Welding
Welding uses high heat to fuse two pieces of metal together. And while welding can be effective in joining two pieces of metal, it does have some setbacks. Because high heat is used, the microstructure of the area that has been welded is actually altered. The welded area can experience a reduction in strength and toughness. Additionally, during the welding process, residual stresses can develop, which further reduce the strength of the metal. Later on, after a piece has been welded, if burnishing tools for metal are used, there may be an increase in metal strength. So because welding can often result in a weakened metal, precautions must be taken. During welding, heat generation and cooling rates must be optimized to ensure as few microstructural changes take place. Furthermore, post-welding treatments can be used to minimize the reduction of strength. But overall, welding can be effective if done right.
Mechanical Joining
Unlike welding, mechanical joining uses mechanical methods to join two pieces of metal, often involving threaded holes. Using screws or nuts and bolts are both common methods of mechanical joining. This method is often used in precision metal finishing because the material sustains mobility after being joined, meaning it can be moved or taken apart easily if needed. Mechanical joining can offer the ability to easily control the quality of the finished product as well as high strength. While there is the risk of the threaded holes sustaining fractures because they can become fatigued if overloaded, there are precautions that can be taken to minimize that risk. Mechanical joints, especially with aluminum components, should be designed with this risk of failure in mind. But because this process is quick, it can be a great option to work towards short lead times.
Properly joining materials is important for the overall manufacturing process, like reaching short lead times, but also for the durability and longevity of the final product. Mechanical joining can often offer more benefits and can result in stronger joinings.