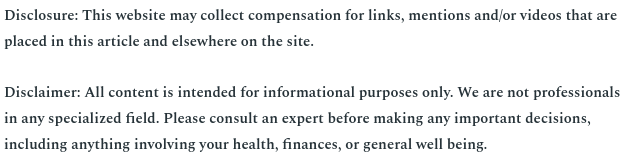
Injection molding creates some of the smallest microcellular parts and pieces needed for automobiles, construction, and other items. Additionally, there is an insert molding magnet that helps to complete the injection process. The process creates prototypes or other items that may come from polyurethane Reaction Injection Molding (RIM) processed materials. With the different materials used in this process, any of them may be cells as small as one-thousandth of an inch.
The Injection Molding Process for Microcellular Systems
Many different processes are able to produce these prototypes and microcellular items. It may be RIM or even the polyurethane injection molding process where there is a combination of two liquid components. In either of these processes, there may be a combination of polyurethane, polyureas, polyisocyanurates, polyester, polyphenol, polyepoxide, and nylon 6. It could be the creation of a fiber mesh or a foamed material, though some of the thicker ones are solids used for walls in construction.
Other Encapsulation Molding Processes
In the same way, encapsulation molding designs mold that will develop some of the smallest parts needed for construction or other industries. Some parts are used for walls developed at about one-eighth of an inch up to one-half an inch. The injection molded enclosure has the ability to help with encapsulation where those parts are intended to fit.
Injection Molding and The Insert Molding Magnet
Many processes work together in order to complete injection molding and the different molding processes such as the reactive encapsulation molding p.rocess. In addition to the process, the addition of the insert molding magnet is able to improve the process. While injection molding may be easily able to make prototype microcellular parts, there is also the to develop a chemical foam that is able to be injected to a capsule or structure that presents the shape of the part to be constructed. Different reaction molding processes are able to make polyurethane and other parts by the creation of a chemical reaction and eventual curing.
In all of these processes, after two liquid components are combined, a chemical reaction is used to create a foam that will be molded into a microcellular part. Incredible pressure is also applied for the finalization of a part construction. Pressure is anywhere from 1500 to 3000psi in order to help create a plastic part from the foam that came out of the chemical reaction.
With all of these different small, or event microcellular, parts are needed for different industries, the ability to create a mold and a prototype with a pressurized foam is a very specific procedure. No matter the process that is chosen, a chemical reaction of different liquids is able to provide the base material to create any number of tiny parts that are able to help with the construction of homes, cars, and many other items.