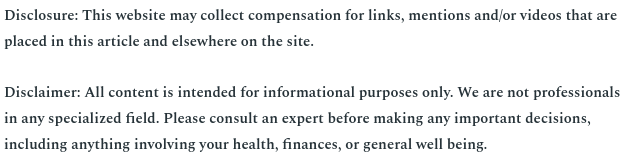

Retention knobs, by definition, are knobs that get screwed into the ends of tool holders and work to lock tools in place within the spindle. Though they are quite small, simple, and seem relatively unimportant on their own, they play a valuable role in the machining and manufacturing industries. Without them, tool holders would fail to be as effective and all kinds of tasks could become inaccurate and inefficient. Those problems could cost businesses time and money that simply can’t be wasted in today’s ultra-competitive marketplace. Because of that, every owner should take the time to make sure they are properly using retention knobs and all kinds of other tools, no matter how small, to help ensure efficiency.
One thing that owners will always have to consider when looking to upgrade with new tools is retention knob dimensions. Though they are quite easy to use, knobs of the wrong size will not be as effective as they could be. Before buying them, owners will have to make sure that they know the exact retention knob dimensions that their machines and tools need. Though that process might be a bit time consuming, it is an important step to take.
Depending on the job and tool, retention knob dimensions could vary significantly. On smaller hand-held tools, they might be no bigger than about a quarter of an inch long while bigger machines might need knobs that are over three inches in length. Proper sizing will be needed to not only make sure knobs fit, but also to prevent them from breaking or wearing down too quickly under harsh environments. So thickness and weight, in addition to length, are also important factors.
Of course, retention knobs aren’t the only tool that workers need to use to work efficiently. In addition, they could need presetters for managing and measuring tools, boring heads for making boring processes easier, and ER collets, which are the most widely used clamping system in the machining industry. All are ineffective on their own, but when added to production systems, they are quite valuable.
Every company is different, and it is unlikely that any two will use the exact same set of tools for production. However, taking the time to find and invest in the proper ones is a necessary task for every owner. Without doing so, they could run into all kinds of both efficiency and accuracy production. Those issues can be wasteful and crippling, so working to avoid them is always a necessity for guaranteeing success.