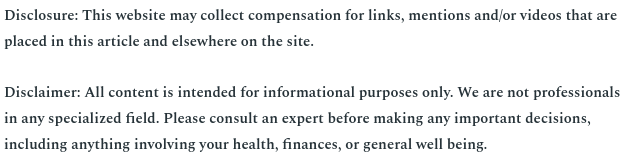
Man Aging medical waste disposal is a crucial aspect of healthcare operations that ensures safety and compliance with regulations. Understanding the types of hazardous waste is essential for anyone involved in healthcare, as improper disposal can lead to serious environmental and health risks. In medical settings, you often encounter both hazardous and nonhazardous waste. It’s vital to distinguish between the two to prevent contamination and to ensure that each type of waste is handled appropriately.
For example, hazardous waste samples might include items like used syringes, contaminated gloves, or anything that has come into contact with infectious materials. Proper disposal of these items helps protect not only healthcare workers but also the wider community from potential harm. For those involved in hazardous materials operations, staying informed about the correct procedures for handling and disposing of waste is critical. These operations require specialized training and knowledge to safely manage the risks associated with hazardous waste.
By adhering to the best practices for medical waste disposal and understanding the nuances of hazardous and nonhazardous waste, you help maintain a safe environment for everyone. Proper disposal practices not only comply with legal requirements but also demonstrate a commitment to public health and environmental responsibility. Check out the options that are available to you today!
Not all aspects of industry is clean. Toxic sludge, bio hazards, disease, radiation, flammable gases and liquids, and more are a reality for some industries, and hazat materials are indeed hazardous materials, so working with hazardous wastes should always be done right to prevent illness, poisoning, or worse. Hazmat certification is the result of required training for shipping hazmat materials, as well as handling them in the workplace. For one example, flammable liquids, most often gasoline, make up the bulk of transported hazardous materials in the United States at 86.4% by value, 85.4% by weight, and 66.5% by ton-miles. Whatever a worker deals with, the right training and equipment is the best way to avoid disaster, and required training for shipping hazmat materials is a good first step.
There is a solid industry for handling hazardous wastes, despite the dangers associated with it. For one thing, in the year 2016, the removal of hazardous materials earned a median salary of $40,640 for workers, and there’s plenty of waste to handle: just over three billion tons of hazardous materials area shipped each and every year, a lot of them flammable gasoline. In particular, Texas is the American state that produces the most oil, and as an example, in 2016, that state produced 1.176 billion barrels of oil. That accounts for 44.3% of the total oil production in the United States alone. There is little doubt that required training for shipping hazmat materials would be common in that state, especially on trucks. In fact, for all hazmat shipments every day, 94% of it is done by truck. Requirements for handling hazardous wastes are strict, and for good reason. There are several clear, essential steps to take for proper hazmat handling, whether by truck or on the worksite.
Hazmat Materials and You
OSHA, or Occupational Safety and Health Administration, typically mandates that hazmat workers complete 40 hours of hazmat training, and some of these workers ma be required to have state specific licenses for this job, depending on where they live and work. According to DMV, some states, such as Kentucky, New York, and Texas, require applicants to apply first at their local DMV rather than online or at an application center. What is more, applicants must also pass a written exam, complete medical screening, and completing a hazardous material endorsement application. A valid driver’s license of the proper class, completing a TSA background check, and being a legal U.S. Citizen are further requirements.
After required training for shipping hazmat materials, there are established guidelines for workers to follow while on the job. According to EHS Daily Advisor, being cautious, planning ahead, and accounting for what could go wrong can go a long way to preventing accidents or injury. Also, using proper personal protection equipment, or PPE, as well as inspecting it, is crucial. Damaged suits and components should be replaced at once, and only functional ones used.
Also, all materials should be clearly and correctly labeled, and materials should never be put into the wrong container. If material is found in the wrong container, it should not be used, and instead this problem should be reported to the correct supervisors or managers. Similarly, materials should be stored securely and according to their labels’ directions, taking care not to put materials somewhere too hot or cold, or somewhere with the wrong air pressure. And, of course, all hazmat materials should be used only as intended, and never as substitutes for one another or for other materials. Finally, hygiene should be observed: no worker should eat or drink anything while handling hazmat materials, and work stations should be cleaned well after use, and workers should wash their hands after work with hazmat materials of any kind. If all these steps are followed, workplace accidents can remain strictly in theory, and a safe workplace is completely possible.