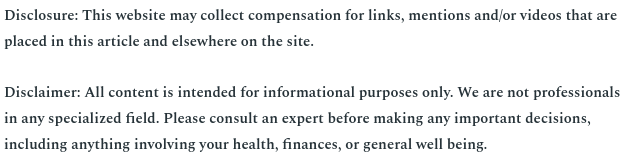

Blow molding is used in many industries today. In fact, many of the items that you pick up from the local grocery store were created with blow molding techniques. Additionally, there are many different methods of blow molding and each of the techniques is important in creating a plastics product that is customized and fit for its storage purpose. These are some of the most common types of blow molding.
Standard blow molding process
The standard blow molding process is the generic design process. It does not include the extras that many of the other techniques do. This results in the most basic of plastics products and containers. In comparison to the extrusion blow molding process, for example, you are left with generic industrial plastic bottles, without any unique designs. A standard blow molding machine consists of three major parts, the extruder, accumulator die, and molds from which containers with different shapes and sizes are processed. However, more complex of containers and shapes often require more advanced of blow molding techniques, such as the extrusion blow molding process.
Injection blow molding process
The injection blow molding process is primarily used in large quantities. It is often used to create a plastics product that is inflated and the inside is hollow. An example of this type of plastic would be soda bottles. The bottle is carefully designed to fit consumer?s hands, while the inside is hollow to effectively hold the soda content. This blow mold design is used for many products, including detergents, cleaners, and water bottles. Additionally, the designs are created and hollowed to hold different amounts of contents.
Interestingly, plastics and their ability to have hollow interiors make them one of the most efficient products on the planet. Just 2 pounds of plastic can deliver about 1,300 ounces, or roughly 10 gallons, of a beverage such as juice, soda, or water. You would need about 3 pounds of aluminum to bring home the same amount of product, 8 pounds of steel, or over 40 pounds of glass.
Extrusion blow molding process
The extrusion blow molding process is probably the most complex of all the methods in making plastic bottles. This custom blow molding process uses hollow tubes, rather than hollow bottles. The tube is inflated and then cooled to create the final plastics product. As of today, the manufacturing companies could choose between the extrusion blow molding process, injection blow molding, and stretch blow molding as three methods of this specific industrial process.
How the specific process is chosen
With so many blow molding processes available, how do manufacturers decide which one to use? The decision process is often complex and includes many variables. Additionally, the business itself will sometimes have a say into the specific blow molding technique that is used, based on the final intended project. It is also important to note that some manufacturers only specialize in one or two of the blow molding techniques, making the decision easier. Finally, the consumer?s preferences and expectations are also factored into the specific type of blow molding used and the final product.
Blow molding processes are used to create different plastics products. Plastics are an extremely important part of our consumerism industry. The majority of products that we bring home were created or packaged with plastics in some form. With numerous blow molding processes to choose from, we are left with different style of plastics products. A lot of decision making and design thought goes into this process at the manufacturing and industrial level.