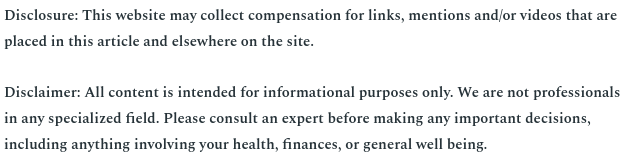
When it comes to manufacturing, all companies are always looking for the next big innovation. One way for companies to increase their value and be more efficient. One way to do this is with lean manufacturing engineering.
There are five core principles of lean manufacturing engineering, which include:
- Value: One of the core tenants of lean manufacturing engineering is having an understanding of what the average customer assigns value to, especially when it comes to services and different projects. By finding and then understanding what a customer assigns value to, organizations can determine a top-down cost to produce their products and services. It’s all about eliminating waste and maximizing customer value.
- Flow: To eliminate waste in lean manufacturing engineering, companies must understand flow. When value stream stops, waste happens. In lean manufacturing engineering, flow is essential in creating a value chain where there are no interruptions in the production process. Essentially what you’re looking for is a system where all the parts and processes work in harmony with each other.
- Value stream: Value stream in lean manufacturing engineering refers to the entirety of a product’s life cycle; from the time it’s a pile of raw materials to when it’s turned into a product for sale to customers. Before anything is produced, companies have to determine their processes and figure out where the value is. Anything that doesn’t add value is eliminated. Traditionally, value stream mapping will reveal three types of waste: steps that unambiguously create value, steps that create no value, but are unavoidable and steps that create no value and can be avoided.
- Pull: This principle helps ensure better flow by making sure no products are produced ahead of time, which creates large inventories and stops work flow. Essentially, the idea is that no products or services are produced until they are ordered by customers. This requires companies to be flexible, be efficient with communication and be good with short design to create the best value possible.
- Perfection: The ultimate goal of lean manufacturing engineering is perfection. That is achieved by continually improving the steps in the production process. The pursuit of perfection allows companies to stay ahead of their competition and to not take any step in the process for granted.
Along with a perfect manufacturing process, companies need to have an efficient factory layout. Poor factory layout can easily lead to a production decrease and a loss of profit. An effectively factor layout has many advantages, which include:
- Decreased labor costs
- An increase in production, which means products are produced and delivered on time
- Equipment running more efficiently
- A decrease in workplace accidents
- Fewer maintenance costs
Bottom line: good factory layout will make a business more efficient. With that in mind, here a few tips for improving factory layout and revolutionizing how your company does business:
- Review what your current layout is: One of the most important things a company must do to improve its production is take a look at the current layout and look for where the issues are. That means looking at absolutely everything, leaving no stone unturned.
- Collaborating: Another way to improve factory layout and efficiency is to collaborate. There’s a lot to be said for seeking out and listening to a lot of voices. In this vein, one option is to hire a manufacturing consulting form. Believe it or not, there are more than 700,000 consulting firms that deal with all kinds of manufacturing aspects; everything from process design and layout to facility design. Collaboration also means talking to employees at all levels and listening to whatever concerns they have. Rank-and-file employees are the ones who are at the heart of production, so they’ll be able to tell managers where the issues are. They can offer insights that managers and CEOs might not see if they’re not in the think of it on the factory floor.
By using the principles of lean manufacturing engineering and reviewing its factory layout, companies can make their production methods more efficient and focus more on the needs of their customers. By reviewing layouts and collaborating, companies can identify where there are issues in production and fix them or totally eliminate them if they are deemed unnecessary.