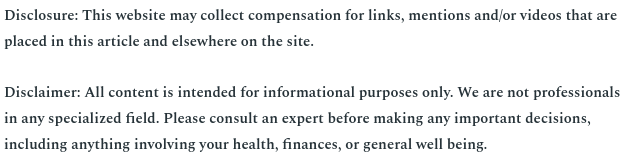

The application of a specific torque to a nut, bolt or other fastener is typically done with a torque wrench, an instrument developed by Conrad Bahr in 1918. He was working for the New York City Water Department at the time. Calibration of any instrument requires the comparison of two instruments. You should know the correctness or magnitude of one and the other is the one you are measuring. The primary and secondary elements will determine the type of load cell used to sense the force. These are hydraulic load cells, diaphragm load cells, gauge load cells, spool type load cells and ring type load cells. At the end of the day, it is important to pay attention to your torque analyzers and torque control program.
- How important is torque control? The fatigue strength of the materials being used in manufacturing has a direct impact on the reliability of any machine parts that are subject to loads and stress levels that do not remain constant. Threaded fasteners rely on an interaction that is elastic that happens between the components. The tension that is keeping parts together needs to be stronger than the force that is trying to separate them. When this is the case, the bolt (or other fastener) will be nearly totally immune to fatigue. The way to maintain this is to apply the correct level or torque, therefore the reliability and accuracy of your torque analyzers is very important.
- Make sure you use the right tool for torque. You have a lot of options when it comes to tools for measure the toque you will apply to your fasteners. There are electric screwdrivers and then these tools go all the way up to industrial torque wrenches that are much larger. You can also use toque multipliers and pneumatic tools. The calibrated torque setting mechanisms can be set in the factory or you can set them. When you have reached your desired setting, the tool will give you some sign that you are there. A lot goes into picking the right torque tool so you should do some research before you do this. It is worth the extra effort to learn as much as you can about your different options before you make a decision. You may want to go as far as to get a product demonstration, which can be very helpful.
- You need a rigorous torque calibration program. When you want to fine tune your torque control process you calibrate everything. Torque tools are precision instruments that need to be maintained and stored like fine measuring tools. These torque analyzers are critical to any torque calibration program. You need to calibrate your torque analyzers on a regular basis to maintain their accuracy, which is the whole point of the program that you will put in place. When you calibrate regularly, you can correct any problems when they are small. It is normal for some slippage to happen over time and does not indicate any problem with your equipment or instruments. This slippage is just something that should be watched and taken care of as it happens. Different companies have different schedules for their calibration, the time intervals between calibrations runs from six to 12 months. You need to use the schedule that works best for you and your needs.
- An ounce of prevention is worth a pound of cure. When you are working with your torque analyzers, you need to check your instruments regularly to see if there are worn or broken parts. This preventative maintenance will save you time and money in the long run. Do not scrimp when it comes to this because it can make a big difference in keeping your torque tools accurate and will make sure they are performing at the level you need them to perform. One way to do this is to set a schedule for proper maintenance of your torque analyzers. Each tool should have its own maintenance schedule because slippage happens at different rates for different tools.
It is hard to overstate the importance of properly maintaining your torque analyzers. Maintaining their performance and accuracy will have a direct impact on your bottom line.
andnbsp;