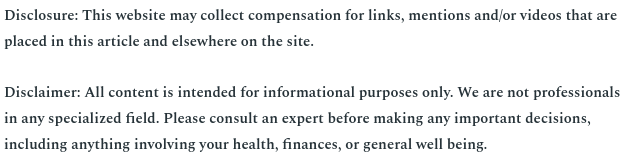

What makes one printed circuit board effective and the other a liability waiting to happen? How can you ensure your prototype PCB manufacturing company is delivering regular quality on a constant basis with no customer left unsatisfied? As the saying goes, knowledge is power. Knowing a little bit about PCB layout can help immensely with overseeing your prototype PCB manufacturing services and making sure that you’re covering all the basics that go into this common piece of everyday hardware.
The printed circuit board industry has done nothing but thrive these past few years. When you consider the prevalence of technology in people’s lives, it makes sense that more and more are having a difficult time living without a high-quality cell phone, home computer or security system. When your company wants to provide them with tools that they can count on, learning about what goes into a PCB will make sure no detail is left unexplored.
Let’s learn about how the printed circuit board is made. The first stage of the process is creating a stencil for both engineers and machine assemblies to follow. Framed stencils generally have smooth aperture walls and can be used for 16 Mil pitch and below for what’s known as the Micro BGA. Once the stencil is complete, the printing process can begin.
No matter your preference, there’s a method perfect for your company’s PCB design and layout needs. The three most common (which include everything from the component designators to switch settings) are silk screen printing, liquid photo imaging and ink jet printing. These need to have every last bit of information available to make sure the printed circuit board that appears at the end of the assembly line is up to your customers’ high standards.
There are two commonly used types of circuit assemblies related to the printed circuit board. You have the integrated circuit (which is sometimes known as a microchip, a common vernacular in many circles) and the hybrid circuit. Your PCB manufacturer should be able to provide both of the same quality, letting you address a wider variety of customers in your field.
Last, but certainly not least, we have the final part of the prototype PCB manufacturing process. Laminates are created by curing under both pressurized and heated layers of cloth to create the most uniform thickness imaginable. The size can be up to four by eight feet in width and length, though many PCBs are much smaller in design. Although the temperature marker material is initially opaque, it will liquefy and become shiny once it surpasses 400 degrees Fahrenheit.
It’s important to know about what causes a quick turn PCB process to fail. The most common contributors to a lackluster product are these two factors — you have performance problems caused by environmental stresses as well as issues with the production process. Although machinery has done a fantastic job of increasing productivity and reducing error, a human hand is still needed to oversee the process. The best PCB company is one that combines the ingenuity of engineers and artists alongside an up-to-date assembly line.
Just because quick turn PCB prototypes are incredibly fast doesn’t mean they’re sloppy. How will this knowledge help your brand going forward? There’s only one way to find out.