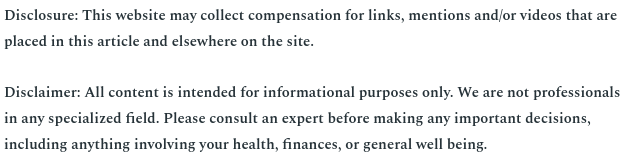
The construction of machinery and other items that consist primarily of metals can be a tricky operation. While many people assume that all metal is essentially created equal, that is not the case whatsoever. The quality of the metal varies considerably, and it is a major determining factor in the long-term functionality of the component that depends on it. Getting the right metal parts is therefore crucial when building anything. But this can be challenge. Often, the most accessible and least expensive metal parts are those that are going to break on you. However, there are some things to keep in mind whether you’re buying items consisting of metal parts or supply the metal parts for manufacture that will make the final product one that lasts longer and be a better choice for consumers.
Be Sure the Solution Fits the Application
When putting together an idea, it’s easy to think more about the purpose of the mechanism than the details of how it is going to be constructed. But this can cause serious problems. For instance, if you are building a machine meant for the general public, there are safety concerns involved. The mechanism, as well as its parts, need to be safe for children as well as others with physical limitations. If the metal parts that make up the product are not of high enough quality, it may break. This could result in endangering those who purchase it. Therefore, you need to consider the type of metal used carefully.
That’s not to say that every machine or product that has metal is bound to deteriorate in a short period of time. Using the right kinds of metal can extend the life of many products. For example, some products claim to be “rust-proof” or made of stainless steel, yet the metals used are not fit to stand up against the salty air near the coast.
If you are manufacturing something that may be purchased by people living in one of these areas, you would be wise to take this into consideration. This could also represent the potential for more profit. If you’re able to choose the right metals, you can advertise your product as one that is “coast weather-resistant.” You would the earn the business of coastal residents who are sick of their things being eaten away by the atmosphere.
Make Sure the Right Processes Are Used
For many metal applications, an induction furnace is the best option. It combines effective heat with efficiency to help produce metal products that last. The strength of a product forged in an induction furnace is enhanced by the process of induction melting. An induction melting furnace is able to melt metals to be reformed, cast, or combined with others to create a stronger end product. Spare parts that aren’t used in other processes can also be melted in an induction furnace.
Induction heating equipment helps get materials to an adequate melting point. When they are sufficiently melted, it is easier for them to combine with other materials to for a new, solid component. Without adequate copper melting, steel melting, or other type of forging process, there’s a good chance that the combined elements will not bond well enough together to produce a reliable component. This could significantly degrade the quality of the end product. It may also endanger the safety of the product. Understanding how your products pieces are made in an induction furnace can help give you confidence as you use them or sell them to others.
Do What’s Best for the Environment
Even though profits often have to take first priority, we shouldn’t ignore the environment. The right metal melting furnace can be efficient enough to spare the environment from unnecessary waste. The fuels used to heat up metal have to be provided and consumed in great quantities in order to produce adequate heat. You will want to be careful that you have modern equipment that runs efficiently in order to do what’s best for your business and the environment.
With the right materials and a thoughtful, well-planned process, you can confidently produce the kinds of parts you and your customers will benefit from for years to come. Check the quality of the induction furnace and the process in general before committing to a supplier.