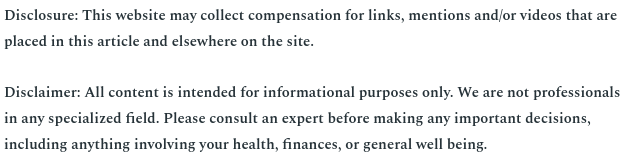

American workplaces today are safer today than ever before. Companies do more to protect their staff from injuries on the job that at any time in recorded history. As a result, the number of injuries workers suffer on the job are way down. In 1972, there are about 11 injuries per 100 workers. In 2011, the number was down to only 3.4 pre 100 people. To keep workers safe, the Occupational Safety and Health Administration (OSHA) has very specific guidelines that businesses need to follow. These cover everything from worker trainings to equipment requirements. For example, OSHA has very specific guidelines for rigging supplies.
Keep Your Workers Safe with These Tips
- Plan to do your work safely. There is saying that says, “A failure to plan is a plan to fail.” If you carefully plan how your employees will get a job done safely, the chances are they will. This means, plan and map out all of the steps that will be taken to complete a project. This should be detailed and include designating who is responsible for each task and step in the process. Write up a checklist and include which team members will be involved in each step. When preparing a budget for any job, make sure you include the costs of any safety systems such as fall protection equipment.
- Equip your workers correctly. Make sure you have the right equipment for the job. Get the right rigging supplies for jobs where it is required. Falls can be very dangerous. An unsecured person can fall nearly seven feet in about two-thirds of a second. The good news is that this can be prevented with the right safety equipment. Safety nets offer great protection to workers, especially in areas where there is a possibility they could fall more than 25 feet. Make sure your scaffolding and ladders are the right dimensions for the job and project. Workers who are stationed at six feet or more above the ground are at risk for a major injury or even death without the proper safety equipment.
- Make sure all staff are properly trained. All sorts of workplace injuries can be prevented with the proper training. Workers need to be trained on the specific equipment they will be using for their jobs. If you have someone working with rigging supplies, they should have the proper rigging certification, for example. Companies are also required to train all their employees to use all the kinds of safety equipment and other systems that they may encounter while working. This includes the rigging supplies but also scaffolding, fall protection gear and anything else they may need to use. They need to be able to recognize dangerous materials and settings when they see them. Providing fall arrest training to all of your staff is one great way to prevent falls in the workplace.
Businesses can offer in house trainings or send their employees to an outside form or even to OSHA offices. osha fall protection training is offered all around the country. It is important to train new hires (or verify they have been trained) but also to conduct additional trainings as the technology advances, changes in procedure are implemented and just periodically to keep people up to speed. It never hurts to brush up people’s skills, especially on rigging supplies they may not use as frequently, for example.
Another good idea is to have a plan for what your staff should do during an emergency such as a fire or natural disaster. You should have drills for things that you anticipate happening or general evacuation drills for events that you cannot anticipate. Having plans for what you will do if a staff member, or more than one, is injured on the job will help reduce or eliminate any panic or confusion that might otherwise arise.
Remind your staff that safety is everyone’s job. From the person who owns and runs the business to the most recent person who was hired, safety is something everyone should care about. It is as critical the company’s bottom line as anything else you do from sales, to public relations and customer service and anything in between. A safe workplace is a productive one.