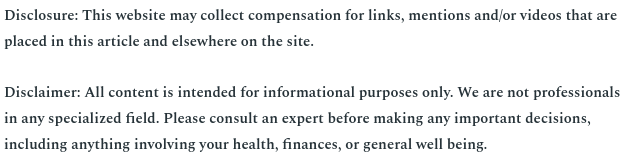
The modern construction industry is a truly vast one, and the American construction industry alone is worth over $1 trillion, an impressive total. Many construction firms large and small can pool their resources and workers to create just about anything, from factories to schools, to warehouses and offices and libraries. A construction zone will be a familiar sight to most Americans, but this is not the only way to make a building. Modular rooms and offices are a more resource-efficient and timely way to construct a building, and the same is true for making warehouse offices and mobile offices for construction firms. What is there to know about modular office buildings and prefab tech, and the uses for warehouse partition systems? All-in-one, mobile warehouse offices are in demand for a reason, after all.
All About Prefab and Modular Construction Methods
Ordinarily, construction workers will gather on the project site and erect a building, but modular construction methods favor indoor, remote work. As opposed to an open project site, modular construction firms build rooms indoors in a factory, which protects the in-progress room and the workers alike from the elements. More importantly, these indoor construction methods are somewhat faster than traditional construction work, and they are a lot more resource-efficient, too. Many industries today are looking for ways to reduce waste, especially for resources like wood or metal or plastic, and modular warehouse offices and hotel rooms are quite efficient to make indeed. Leftover or scrap materials can easily be reclaimed, and this eliminates the need for hiring junk removal services (as regular construction project managers often do).
How efficient is the construction of warehouse offices or modular hotel rooms? The Building Industry Association of Philadelphia, for one, reported that prefab and modular construction can reduce overall waste by 9-20% or so. Meanwhile, the UK-based WRAP (Waste and Resources Action Programme) says that modular construction can reduce waste up to 90% for certain materials. This includes timber, bricks, concrete and cement, shrink wrap, wood pallets, and even cardboard and plasterboard.
Modular offices and rooms are quick and efficient to make, and once complete, they can be shipped to the project site and simply put in place with minimal effort. Modern warehouse offices can be set down wherever they are needed, and modular rooms for a skyscraper or hotel can be installed quickly, since they already have their utilities in place (electrical wiring, plumbing, etc). They are low-maintenance to install and run once the building is complete. So, it is little wonder that this new technology is proving so popular across the United States and beyond. Around 90% of engineers, 84% of contractors, and around 76% of all architects say that they use prefab and modular technology for at least some of their projects, if not all. In a 2011 survey, respondents explained what sort of projects they like to use modular tech to build, and 49% of respondents said that they build healthcare facilities this way. Meanwhile, 42% of respondents also reported using prefab/modular methods to make manufacturing facilities, and 42% also use these method to construct college buildings. And in 2017, Marriott International once pledged to use modular tech for 13% of all of its North American projects.
Modular Offices and Walls for Warehouses
Buildings can have modular offices, break rooms, hotel rooms, and bathrooms installed, but what about warehouses? These buildings make relatively little use of permanent walls, instead favoring modular partitions, walls, doors, and storage areas to accommodate just about any stock items that arrive and need storage solutions. So, a warehouse manager can choose from various warehouse offices and have one brought to the warehouse, and placed right there in the main area for convenience. From there, the manager can easily see what’s going on and interact with workers without much trouble. Meanwhile, fully prefabricated walls and warehouse partitions can be purchased and installed anywhere they are needed, to make temporary storage rooms that can be taken down or adjusted at any time. They even come furnished with doors and windows on them, among other features, to make storage rooms or offices. Wire storage cages can also be set up around the warehouse, and they are easily relocated or removed at any time.