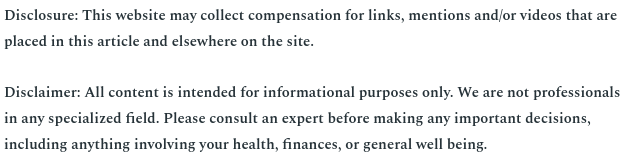
Pottery is a great hobby that many take on to relax from their daily lives—some people require a level of relaxation that most pastimes can’t provide besides pottery. The art of pottery allows individuals to fully immerse themselves through an artistic means to create designs that are life-long that can become a treasured piece or a gift to loved ones. However, pottery consists of logistics that allow for pottery to come out beautifully—understanding the methods of pottery provides for the creative process to be respected and taken in awe by many.
How To Reduce Firing Times
Reduction firing creates some of the most breathtaking color-patterns in pottery; this is brought about through reduction. The high-level fire gazes that are used to mold pottery requires reduction, and otherwise won’t yield successful results in neutral or oxidation firings. The trick in pottery is each fuel-fired kin fire differently. Therefore it could take a considerable amount of time to figure out what works best for each fuel-fired kin. One of the first things you should understand is the differences in kilns—there are a variety of materials a kiln can be fueled by, each yielding different results. The concept of kilns dated back to around 6,000 BCE and fired an upwards of 900 degrees Celsius. (1,653 degrees Fahrenheit) Kilns were popularized as a method for pottery because its elements can typically last an upwards of 100 firings and the average kiln can become as hot as 1,800 to 2,400 degrees Fahrenheit.
Reduction firings can only be performed in a fuel-fired kiln to ensure safety for its users—if it’s an experienced potter, certain exceptions can be made, like using spray cement coating because they understand the full logistics and restrictions that come with using advanced techniques, like staggers. Typically, an appropriately fueled kiln uses natural gas, propane, wood, and oil to yield proper pottery designs that’ll withstand certain amounts of weight—the coating is a strong determinate of its molding as well, a spray cement coating would produce far different results than a coating of cement.
How To Put A Kiln In Reduction
1. To start the reduction cycle make sure to see the witness cone before the target cone begins to tip. Typically, a cone pack comes with at least six cones, be sure to start the reduction process when cone 4 starts to tip.
2. Make sure to build up a considerable amount of pressure in the kiln, then partially close dampers in the chimney to reduce the opening in the exit area.
3. Finally, reduce the amount of air drawn into the kiln—slow the blowers down, decrease the air opening in the venturi burner, or place some ceramic fiber or blanket into the port opening.
A Quick Guide To Pottery Basics
Pottery requires working with your hands, specifically clay. Fortunately, building small pieces out of clay by hand and modeling them through a potter’s wheel is easier by using spray cement coating. The tools required in pottery are often used in both disciplines, that makes it a versatile hobby and relatively easy to figure out, such as spray cement coating. However, there are a few basic methods that require a high level of precision and focus on creating extraordinary works.
1. There are a few methods that benefit optimal clay making to create great works. When a kiln reaches around 660 F, water becomes chemically-bonded water and starts to be driven off—the clay reaches around 930F, and it becomes completely dehydrated, creating a permanent ceramic coating or cement coating that can hold and shape the molding appropriately.
2. The bisque firing method requires the kiln to reach approximately 1730 Fahrenheit, allowing the pot to make a powdery material that transformed a semi-fragile element while the high temp ceramic coating remains porous enough the recommendation application of glazes.
3. After the desired temperature of the ceramic insulation coating has been achieved, the kiln is turned off. The cooling process is simplified through a thermal insulating coating that allows the mold to maintain a consistent temperature, avoiding the stress of a temperature change.
4. There are 5 types of ITC ceramic coatings: ITC 148, ITC 100HT ceramic coating, ITC 213 ceramic coating for metals, ITC 296A ceramic top coating, and ITC 200 EZ ceramic repair.