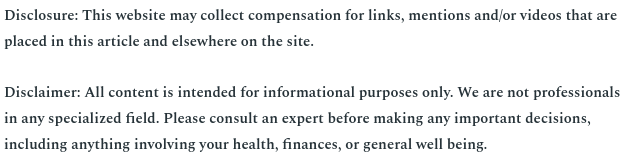
Modern manufacturing involves many different processes. There is a lot more to it than sawing wood or welding metal, since other processes such as burr removal, laser cutting and etching, sanding, and coating are involved as well, and that includes liquid powder coating. But what is liquid powder coating, and why get a powder coating on a product? Companies are always looking for the most price efficient and resource efficient methods for getting work done, and liquid coating services are a promising option to take. Often used as an alternative for regular paint, liquid powder coating can finish a product’s surface and make it look nice, minus the drawbacks and limitations of conventional paint jobs. While this method has not and probably never will totally replace paint, it does have some perks, and the industry is strong and still expanding. Now, how does it work?
Liquid Powder Coating Basics
Liquid powder coating is one of the last steps taken in manufacturing a product, often used on metal surfaces such as for appliances or bicycles, or even cars. This is a major part of the overall finishing market; in fact, by now, powder coating (as a dry finishing process) makes up just over 15% of the total industrial finishing market. The overall market is due to reach a total value of $12.48 billion by the end of the year 2020, and from 2016 to 2021, according to experts, the coating industry’s demand should grow 3% per year (on average) in the United States. In particular, household appliances are often coated this way; it’s the largest single part of the powder coating industry, making up about one third of all items that are coated in such a manner. Furniture is also getting treated this way more and more, and so are automobiles. Estimates say that the market for powdering furniture this way should grow around 7.6% in the foreseeable future.
Why use the liquid powder coating process at all? What does it offer over paint? Take note that these materials are classified as 100% solid, but they do not require any solvents in their formulation, setting them apart from regular liquid coatings like paint. What is more, liquid powder coating does not contain any significant amounts of VOCs (volatile organic compounds), meaning it compares favorably to regular paints and liquid coating materials. This means that liquid powder coating is environmentally friendly, and that in turn boosts it s demand.
Putting on the Powder Coating
It is clear how efficient and popular liquid powder coating is, but why else might it be used? Liquid powder coats serve two main functions on a product’s surface: decoration (aesthetics) and protection. A coat of powder is smooth, tough, and may be very attractive in color, and won’t flake off or chip off the way old paint will. But it’s not just for looks; liquid powder coating, depending on how it is made and applied, may also shield the product’s surface from UV radiation exposure, not to mention preventing rust.
As for the application process itself, paint brushes are not used. Instead, the powder is electrostatically charged, and then it is sprayed onto the product’s surface with compressed air. The charged powder is attracted to a grounded part, and once that is done, the product is put in an oven, where heat may fully bake the powder onto the product’s surface. It may be noted that the powder cures fairly quickly, which cuts down on work time, and since a relatively low temperature is used to finish the powder coat for non-oven applications, this process can be used for delicate items if need be. The final coat is also quite durable, making it suitable for agricultural and outdoor uses as well as indoor uses.