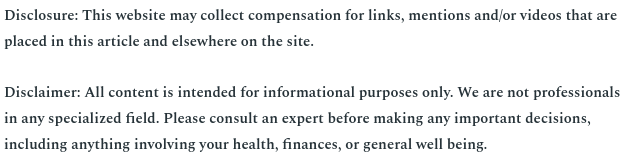
Manufacturers who work on extrusion projects should be careful when choosing the alloy to use. If you need to mold the alloy, one of the best choices you can go with is the long-established 6061 aluminum.
People originally referred to it as alloy 61s when it was first developed in 1935. But in today’s modern world, it is also called structural aluminum. Due to its excellent physical and mechanical properties, chemical composition, and corrosion resistance, it is extremely versatile and suitable for various applications, including thin aluminum strips.
It is, however, particularly well suited for use in applications including the following:
- Production of electrical products
- Construction and building materials
- Plumbing and piping
- Recreational products
Since it’s more of a wrought alloy rather than a casting alloy, it can be forged, rolled, or molded into a wide range of shapes and sizes.
Different Properties of Type 6061 Aluminum
Because of its widespread availability and extensive range of applications, aluminum metal and alloys are used in almost all current industrial processes. An alloy is made of combined metals to improve material qualities.
Alloying is the process of adding certain metallic “alloying” elements to a base metal to give it unique features. Such characteristics include improved strength, corrosion resistance, conductivity, toughness, and so on, or the desired mix of these characteristics.
The strength of this alloy ranges from medium to high. Corrosion resistance, weldability, workability, and machinability are also good. Tempering improves the strength and corrosion resistance of the metal.
Physical Properties
Type 6061 aluminum belongs to the 6xxx aluminum alloys family, including magnesium and silicon alloys as the principal alloying components. The basic aluminum’s impurity control is clearly shown by the second number. When the second digit is a “0,” it means that most of the alloy is commercial aluminum with its current impurity levels. Therefore, tighter controls are not required.
Furthermore, individual alloys are designated by the third and fourth digits. Type 6061 aluminum has a nominal composition of 97.9% Al, 0.6 percent Si, 1.0 percent Mg, 0.2 percent Cr, and 0.28 percent Cu. 6061 aluminum alloy has a density of 2.7 g/cm3 (0.0975 lb/in3). Heat treatable, readily made, weldable, and corrosion resistant, 6061 aluminum alloy is a suitable choice.
Mechanical Properties
The mechanical qualities of 6061 aluminum alloy vary depending on how it is heat-treated or tempered to make it stronger.
The strength ratings for this alloy will be derived from 6061 aluminum alloy (6061-T6) that has been tempered to T6, which is a standard temper for aluminum plate and bar stock. It has a 68.9 GPa (10,000 ksi) modulus of elasticity and a 26 GPa shear modulus (3770 ksi).
Fatigue strength refers to a material’s capacity to withstand breaking under cyclical loading, which involves repeatedly applying tiny stress to the material over time.
This value is important in situations where a part, such as vehicle axles or pistons, is subjected to repeated loading cycles. The fatigue strength of 6061 aluminum alloy is 96.5 MPa (14000 psi), as determined by 500,000,000 cycles of continuous cyclical loading below the yield point.
Corrosion Resistance
When 6061 aluminum alloy is exposed to air or water, it tends to generate an oxide coating that makes it nonreactive with elements that are corrosive to the underlying metal. The extent of corrosion resistance is determined by atmospheric/aqueous conditions; nevertheless, corrosive effects in air/water are typically insignificant at ambient temperatures.
There may be some corrosive effects like pitting when in contact with alkaline soil. However, this is extremely dependent on soil conditions. 6061 is very resistant to corrosion caused by intense nitric acid, ammonia, and ammonium hydroxide. The corrosive effects can be completely eliminated by applying a protective layer on the alloy, which 6061 alloy reacts well to.
Chemical Composition
The 6000 series of alloys include this one. As a result, magnesium and silicon are the primary alloying elements. Magnesium is used to boost strength, whereas silicon is used to lower the melting point of the metal. The rules for the chemical composition of 6061 aluminum may be found here.
Choose 6061 Aluminum for Various Applications
6061 aluminum’s weldability and formability make it suitable for many applications. Thin metal strips made of this material are very durable and highly resistant to corrosion. As a result, manufacturers from different industries always choose a thin sheet metal made of 6061 aluminum.