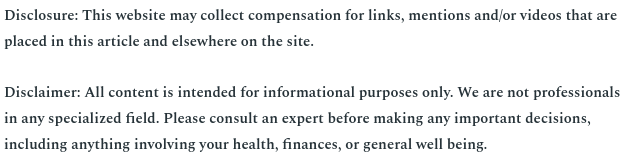
The primary metals most often purchased by consumers include aluminum in bar, tube, sheet, or plate form; hot or cold rolled steel; and stainless steel. Aluminum, in particular, is versatile in its application and widely used in the food and beverage industry because of its ideal properties. There are many aluminum alloys and are available in a range of tempers that are classified in different categories. Each category has its properties and distinguishing physical characteristics that determine its required use across different industries.
Additionally, each class of aluminum alloy anodizes differently which is an important property to consider when choosing an appropriate alloy.
Common Aluminum Alloys and Properties
Aluminum alloys come in a range of series and grades with different properties. They include 1000, 5000, 3003 aluminum alloys which are used for more specific applications while other options like aluminum 6000 and 7000 series.
3003 Aluminum Alloy
This is perhaps the most commonly used alloy thanks to its excellent properties attributed to the mixture of aluminum, copper and manganese — that makes the alloy 20% more stronger than pure aluminum. However, aluminum 3003 alloy is not heat-treatable like other alloys some other techniques can be applied to increase its strength.
Properties of 3003 aluminum include:
- Lightweight
- Moderate strength
- Good atmospheric corrosion resistance
- Easily customizable
Aluminum alloy 3003 welds pretty well with conventional welding methods so it’s easy to work on, unlike other alloys. It also performs much better in terms of mechanical properties than other alloys like the 1000 series. All these properties make 3003 aluminum alloys a preferred and a suitable option for the foodservice industry to avoid chemical corrosion as well as for architectural and other outdoor applications.
Other common applications for aluminum alloy 3003 are:
- Ductwork
- Chemical equipment
- Heat exchangers
- Pressure vessels
- Forming
- Cooking utensils
- Garage
- Mail boxes
- Fan blades
- Gas line and tanks
- Eyelet stock
- Spinning
- Roofing
It has a wide range of applications as it has been strain hardened and partially annealed to enhance its drawing, forming, brazing welding capabilities. The 3003 alloys share the same properties with 3102 alloy
1050 Aluminum Alloy
Like 3003 alloy, this is a non-treatable and a popular grade of aluminum alloy suitable for making automotive parts, HVACR industries as well as the electrical industry. Its properties include superior thermal conductivity and good corrosion resistance. This alloy is applied in sectors such as chemical processing plants, food containers, lamp reflectors, cable sheeting, and ornamental flashings for buildings. Most 1050 alloys are made with an H-14 temper but not annealed like other alloys like 6061 aluminum alloy.
6006/6061 Aluminum Alloy
For quality finishing applications or products like picture frames and premium furniture, 6060 alloys offer excellent capabilities. It’s anodized well than other alloys plus it has excellent corrosion resistance and good surface finish suitable for window frames, pipe, architectural extrusions such as flashing or glazing bars and other outdoor extrusion applications. The 6000 series of aluminum alloy has increasing mechanical properties but their extrusion ability is negatively impacted.
Excellent heat tolerance 6063 alloy is a suitable option for window frames, door frames, shower doors, reflectors, decorative trims, and piping due to its smooth surface and excellent strength. Another alloy in the 6000 series is 6060 and has strong corrosion resistance, ductility, formability, workability and weldability to achieve maximum extrudability. An ideal choice for heat sink profiles.
The 6000 series compose of alloys with good mechanical properties and 6061 and 6005A are considered to be the most with superior mechanical properties. Practical for a variety of applications such as manufacturing of medical equipment, boat components and parts due to its strength and weldability. The two — 6061 and 6005A have similar characteristics — excellent extrudability and strong surface appearance. However, with the increased mechanical properties, the extrudability is compromised and producing thin metal strips becomes a challenge. With leaner alloys like 6060, 6063 and 6005A, you are able to obtain thinner walls and minimum mechanical properties. Choosing the right alloy for your application will optimize your production goals.