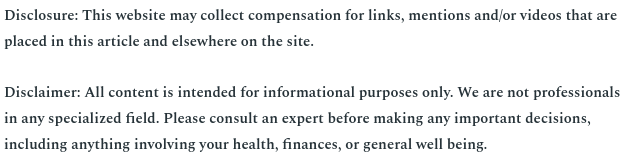

The fact is that some fields are naturally safer than others. For example, an office job might not be quite as hazardous as a job in a manufacturing plant — but that doesn’t mean that the jobs in manufacturing should or can be overlooked by potential employees. Rather, it means that the companies in more hazardous fields simply need to make their environments as safe as possible for their employees. Luckily, there are plenty of ways that they can do so. First of all, there are many different types of equipment developed over the years that make working environments safer. But there are also techniques that all workers can implement to take care of themselves and their coworkers. Many companies now employ things like OSHA fall protection training, which can not only make the workplace more efficient, but safer as well. Unfortunately, some people don’t take training very seriously — and it’s crucial that we change such outlooks. Safety in the workplace isn’t just about taking care of yourself as an individual, but your whole team, and the company you work for at large. Following safety procedures will help you get noticed, and could even be a factor that aids in future raises and promotions. Try to be an example to your fellow employees. Below, we’ll look into a few tips that can help you be safer in your workplace.
Remember Your OSHA Fall Protection Training
Many companies are required to implement OSHA fall protection training. This type of training has been shown to be extremely effective — but it’s only effective if those being trained pay attention, remember, and implement that training at work. OSHA fall protection training usually stresses the three step process that has been proven to prevent dangerous falls and save lives. This process includes planning, providing, and training. Not only does this apply to the higher ups in your company — who naturally are responsible for planning, providing, and training for their employees — but you as well. It’s important that you plan ahead when working on a project that might involve risks, as well as providing the resources that you can for yourself and your fellow employees. You also need to stay up to date on your training, and be diligent about using that training in your field. Furthermore, if you notice corners being cut — for example, if your company doesn’t provide OSHA fall protection training or fall protection certification — you should question the procedures at hand, and are within your rights to do so.
Follow Protocol
When we discuss implementing your training at the workplace, we mean following protocol in real life, not just in the hypothetical situations that may be presented during training. OSHA has a number of different requirements for workplaces that vary depending on the environment of the specific workplace. For example, OSHA requires that fall protection must be provided when there are elevations of four feet in general industry workplaces, five feet in shipyards, six feet in the construction industry, and eight feet in longshoring operations. Furthermore, when fall arrest systems are being tested, OSHA stipulates that a test weight of 300 pounds must be used. This ensures that people in of a variety of different body types — in a variety of different environments — are being protected. The more uniform these procedures are, the more sure we can be of our safety.
Use The Proper Equipment
If a workplace isn’t providing its employees with the proper equipment, the company is in the wrong. But if an employee is given the right equipment but isn’t using it, the employee is breaking important safety rules that are put in place to save lives. Things like wire rope slings, safety nets, and more are there to create a work environment that is not only safe, but efficient. If you don’t use such equipment, you’re only risking your safety and your job, even if it seems faster to work without it.