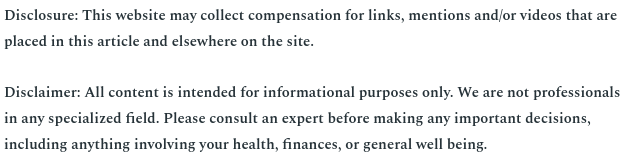

Metalworking can at times be describe as a trade, industry, hobby, or science. Its roots date back millennia, with skilled metalworkers shaping metal for religious artifacts, skilled instruments, and even jewelry. It has grown into an industry of tremendous size, as the skill of metalworking is used for everything from ships and bridges to jewelry making and specific metal parts in engines.
Gardner’s Capital Spending Survey (the largest, most comprehensive survey that details and projects the future spending in the durable goods manufacturing industries) projected that spending on metalcutting would be $8.8 billion in 2015, which is a 37% increase compared to 2014. And most of those who make manufacturing purchases look for products or services at least once per week.
For a company thinking about purchasing new metalworking equipment, it may seem like there are such a wide variety of choices and types that it’s difficult to choose the correct one. Here are descriptions and overviews of two standard metalworking tools that may help guide your decision.
The Drill
A drill, per definition, is a tool with a cutting tool or driving tool attachment that is used to bore holes in material. A drill uses a drill bit or driver bit and typically creates holes that are of a circular cross-section.
There are many types of drills, including the pistol grip drill, hammer drill, and cordless drill. The type of drill you purchase will depend on ease of use and what material you are drilling into. For instance, a rotary hammer drill is used for more substantial material like masonry or concrete.
Drill bits vary in terms of what material they are best used on as well as what their design is. Some, like the indexable drill bit are used for high precision work like computer numeric systems, while others like the gun drill bit are fluted and allow for putting liquid or compressed air into the hole.
The Clamp
The clamp is a fastening device that holds two objects closely together using inward pressure. Clamps can be used for either permanent or temporary holding. Some examples of temporary clamps are band clamps, bar clamps, and the set screw. An example of a permanent clamp is a hose clamp.
The standard ER collet is the most widely used clamping system in the world and specific for metalworking. A collet is a subtype of a chuck that forms a collar around an object and then exerts a strong clamp on that object in it is tightened. ER collets are made from alloy spring steel.
They are ideal for many machining applications, including boring, milling, reaming, tapping, and grinding. Most ER collets feature run out of .0003 inches or less.
When choosing the right metalworking tools for your project, always consider the end of the result of the project and what tools may be most efficient for the job.