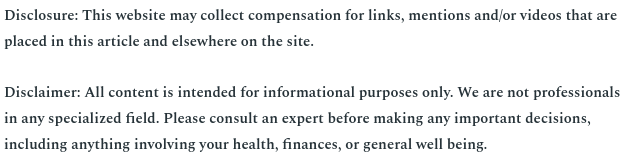
Maintenance has undergone a revolution over the past few decades. In the past, maintenance was performed based primarily on time in service. Air compressor parts that were used for X number of cycles or Y number of days were due for replacement regardless of whether the parts were at or near failure.
This form of maintenance was primarily anticipatory. For example, if a part typically fails after 10,000 hours of service and a 10% safety factor is applied, the part would be replaced at 9,000 hours of service regardless of the actual condition of the part.
This rigid schedule was workable for parts and systems where the cost of replacing parts was far exceeded by the criticality of failure. For example, critical parts and systems on airplanes still rely on this type of maintenance. Even though the cost is very high to replace perfectly usable parts, the cost of an airplane or helicopter crash more than justifies the cost.
However, for less critical systems, this is a wasteful form of maintenance. For example, when most compressor fluids are replaced, more than 99% of the oil that is disposed of was perfectly fit for continued use. This type of maintenance does not take into account many factors that could affect the actual condition of the parts, such as the operating schedule or ambient temperature.
Because of these criticisms, other forms of maintenance were developed that were based on actual conditions rather than assumptions. Here are four steps to reliability centered maintenance:
Identify Critical and Non-critical Parts
To apply the appropriate level of maintenance, you first identify which parts perform critical functions and which parts do not. Specifically, you must identify what happens if a part fails and what effect that failure will have for the rest of the system.
For example, air compressor parts such as pistons, bearings, and valves are necessary for the air compressor to function. The effect of failure means significant downtime to replace or repair the air compressor parts. By contrast, switches and gaskets contribute to the overall functionality of the air compressor but can be easily replaced after failure. The effect of failure means inconvenience or a short downtime, but not more than a minor inconvenience.
Identify Failure Modes
You need to look back on your history and other business histories to determine how the critical parts fail. It is important to identify all the potential failure modes for the next step, so you cannot just say “the part breaks” and move on.
This step may require testing to determine exactly how parts break. Does it break due to physical stress, thermal stress, fatigue, corrosion, deformation, wear, abrasion, or other failure mode? This is where analysis and data collection become important. You might find that many of these occur, with a 50% chance of fatigue, 30% chance of wear, and 20% chance of corrosion. You might also find that although the failure mode is usually fatigue, corrosion plays a significant role by pitting and cracking the part.
Identify Data that Predicts Failure Modes
This is where reliability centered maintenance begins to diverge from rigidly scheduled maintenance. Rather than assuming that a part will fail after a certain amount of time in service, reliability centered maintenance looks for actual predictors of the condition of a part.
Thus, compressor oil analysis may show that the acids and water in oil predict when bearings will fail. This would allow you to use measurements and testing to guide your maintenance schedule rather than sticking to a rigid schedule.
Identify the Steps to Prevent Failure Modes
Rather than replacing bearings every 9,000 hours, you use all of the prior steps to arrive at a maintenance schedule that has a measurable effect on air compressor performance without spending time, labor, and money on replacement parts, unless the data shows that it is necessary.
So, you may find that a compressor oil purifier extends the life of bearings by 20%. You may also find that cracks in the bearing races predict failure within 100 hours. Combining these data points, you can both extend the life of the bearings and only replace bearings when necessary.
Reliability centered maintenance is a data-driven approach to maintaining air compressor parts. It is more economical and reduces downtime for unnecessary maintenance.