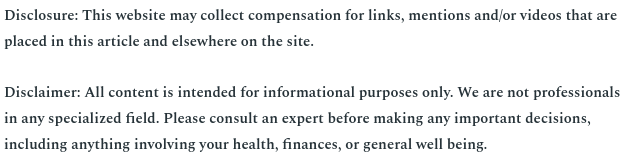
Did you know that the very first known instance of welding occurred all the way back in 3,500 B.C.? Welding is among the oldest human technologies that we know about. That said, safety is just as important today as it was thousands of years ago. Whether you’re entering a welder training program, want to know how to do welding, or are a professional welder, you need to take safety seriously.
If you take some local welding classes, you’ll probably notice that the instructors spend a lot of time discussing safety. Without the right welding safety equipment and practices, you could end up seriously hurt. You might even be blinded or suffer other long-term issues.
Purge monitors and purge equipment can protect you from dangerous gases. Proper ventilation will also protect you from gases. Various administrative and work practice controls, along with engineering controls, can mitigate various welding-related problems and injuries.
At the end of the day, however, personal protective equipment, such as welding face shields and respirators, is perhaps the most important line of defense. When learning all about welding, make sure you pay close attention to safety tips.
The welding industry is older than most people think (the first recorded weld occurred in 3,500 B.C.!), and over its long years there have been a number of tools and equipment invented to assist it. Among these are tools like purge monitors and pipe alignment clamps, which were designed to aid the welder in doing their job successfully.
But while purge monitors and other purge equipment may help keep gases and unwanted air particles away from the welding zones, they do not help keep the welder safe from toxic welding fumes. That is the job of a good ventilation system. However, sometimes the ventilation system isn’t enough, and that’s where these tips can help:
How To Handle Fumes
One of the best ways that one can handle welding fumes is to implement the OSHA guidelines known as the Hierarchy of Controls. These guidelines include practices such as elimination and substitution, engineering controls, administrative and work practice controls, and personal protective equipment (PPE). Let’s take a closer look at each of these practices:
Elimination and Substitution
These are designed to prevent potentially harmful exposures by doing something like switching to shielded metal arc welding (SMAW), or to gas metal arc welding (GMAW) with a solid or metal coated wire. You should take the time to look at the process and find the best way to accomplish your goals with less fume generation.
Engineering Controls
This involves physical changes to the workplace such as isolation (enclosing the welding process), or ventilation. Ventilation is the most common precaution, and there are many ways that it can be done. Natural ventilation, mechanical ventilation, or capturing devices to keep the fumes out of the welder’s breathing zone.

Administrative and Work Practice Controls
These require the welder or the employer to do something themselves, such as re-positioning the head away from the fumes, or moving their body so the air flows back to front. These practices ensure the fumes are pushed away from the welder while they work.
Personal Protection Equipment
Items like NIOSH-approved respirators fall into this category, and each type has a protection factor assigned to them that tells the level of protection that will be given. You should make sure you and your employees inspect these respirators often to ensure they are properly taken care of.
Purge monitors can be a good way to keep unwanted air particles out of your welding zone, but you need to worry about your own health too. Welding is a dangerous job in the wrong circumstances and you should do all you can to avoid that.
